3 IN 1 Details description |
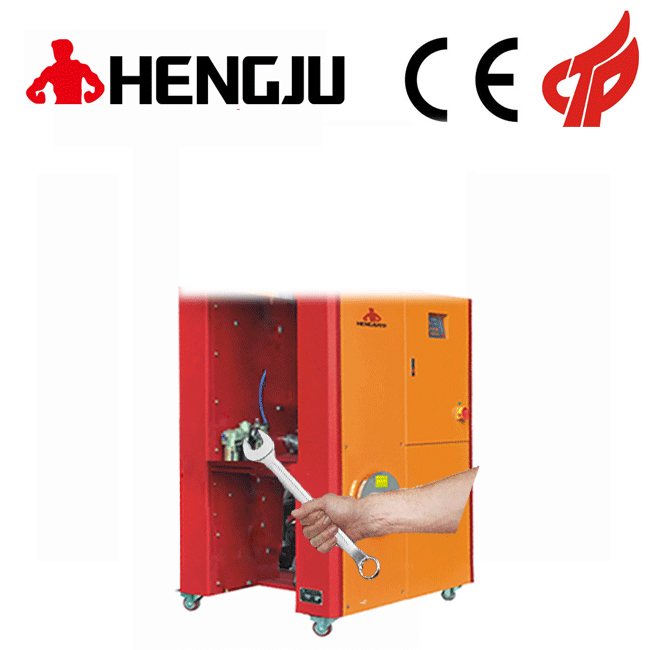 |
product name:3 IN 1 pellet dryer |
release time:2020-11-10 |
Numbering:3 IN 1 pellets dryer-001 |
Brand:wto-btb |
Price:¥By function |
weight :By function |
unit weight:Kg/set |
manufacturer:wto-btb |
patent:wto-btb |
Producing country:china |
simple description:3 IN 1 Compact Dryers |
Product alias:3 IN 1 Compact Dryers,3 IN 1 pellet dryer |
|
3 IN 1 Product introduction |
|
3 IN 1 pellets dryer parameter
3 IN 1 Compact Dryers
Industry standard model |
Technical parameters Model specifications |
Dry weight per time (kg) |
Equipped with motor power(kw) |
Electric heating power(kw) |
Steam consumption (kg/h) |
Cooling area 2 (m ) |
Air volume 3 (m /h) |
Temperature difference (℃) |
With baking tray |
Dimensions (LxWxH)mm |
Equipped with dryer (station) |
RXH-14-B |
CT-I |
120 |
1.1 |
15kw |
20 |
20 |
1400 |
±2 |
48 |
2360×1200×2375 |
2 |
RXH-27-B |
CT-II |
240 |
1.1 |
30kw |
40 |
40 |
5200 |
±2 |
96 |
2360×2200×2370 |
4 |
RXH-41-B |
CT-III |
360 |
2.2 |
45kw |
60 |
80 |
9800 |
±2 |
144 |
3300×2200×2560 |
6 |
RXH-54-B |
CT-IV |
480 |
2.2 |
60kw |
80 |
100 |
9800 |
±2 |
192 |
4250×2200×2560 |
8 |
RXH-7-C |
CT-C-IA |
60 |
0.45 |
9kw |
10 |
10 |
3450 |
±2 |
24 |
1400×1200×2000 |
1 |
RXH-14-C |
CT-C-I |
120 |
0.45 |
15kw |
18 |
20 |
3450 |
±2 |
48 |
2300×1200×2000 |
2 |
RXH-27-C |
CT-C-II |
240 |
0.9 |
30kw |
36 |
40 |
6900 |
±2 |
96 |
2300×2200×2000 |
4 |
RXH-41-C |
CT-C-III |
360 |
1.35 |
45kw |
54 |
80 |
10350 |
±2 |
144 |
2300×3220×2000 |
6 |
RXH-54-C |
CT-C-IV |
480 |
1.8 |
60kw |
72 |
100 |
13800 |
±2 |
192 |
4460×2200×2290 |
8 |
RXH-5-C |
CT-C-O |
30 |
0.45 |
9kw |
5 |
5 |
3450 |
±2 |
8 |
1460×1100×1750 |
1 |
Model |
Capacity(kg) |
Heater(kw) |
Blower(w) |
Overall Dimensions(cm) |
Model suitable |
Weight(kg) |
MHD-12E |
12 |
1.8 |
50 |
65X40X85 |
1oz |
25 |
MHD-25E |
25 |
3 |
90 |
75X50X105 |
3oz |
35 |
MHD-50E |
50 |
3.9 |
100 |
90X55X120 |
5-8oz |
45 |
MHD-75E |
75 |
3.9 |
100 |
95X60X130 |
8-10oz |
50 |
MHD-100E |
100 |
6 |
250 |
100X70X140 |
10-20oz |
70 |
MHD-150E |
150 |
6 |
350 |
110X75X160 |
15-20oz |
80 |
MHD-200E |
200 |
12 |
350 |
120X85X170 |
20-30oz |
120 |
MHD-300E |
3300 |
15 |
350 |
145X100X185 |
25-30oz |
120 |
MHD-400E |
400 |
18 |
550 |
150X105X200 |
30-40oz |
230 |
MHD-500E |
500 |
21 |
750 |
150X105X210 |
40-50oz |
250 |
MHD-600E |
600 |
21 |
750 |
150X105X220 |
40-50oz |
250 |
MHD-800E |
800 |
27 |
750 |
150X110X240 |
50-60oz |
300 |
MHD-1000E |
1000 |
30 |
1100 |
185X135X270 |
60oz以上 |
400 |
MHD-2000E |
2000 |
60 |
5500 |
1480X1800X3600 |
60oz以上 |
780 |
MHD-3000E |
3000 |
64 |
7500 |
1600X2010X4050 |
60oz |
1150 |
Product alias:3 IN 1 material mixture dryer,3 IN 1 pellet polymer dryer |
3 IN 1 pellet dryer Equipment principle
3 IN 1 pellet dryer 3 IN 1 Compact Dryers Dehumidification and drying part: The hot and humid air coming back from the drying barrel is cooled and blown into the honeycomb runner. The moisture in the air is absorbed by the runner and then desorbed by the regenerated heated air. The two airflows act on the runner at the same time, and with the rotation of the runner, the moisture in the air is continuously adsorbed and then desorbed by the regeneration air to be discharged, forming a stable low dew point air, which is heated to plastic The drying temperature is blown into the drying barrel to form a closed cycle to dry the raw materials. Suction part: Suction material is sucked into the dry bucket from the storage bucket or other storage silo container. When the reed switch of the vacuum hopper detects that there is no material, the suction motor runs to generate vacuum in the vacuum hopper. The raw materials in the storage bucket are sucked into the vacuum hopper due to the air pressure difference. When the suction time is completed, the suction motor stops running, and the raw materials fall into the drying bucket due to their own weight. The dried raw materials are pumped from the drying barrel to the electric eye hopper installed in the plastic molding machine. This is a mechanical equipment used for automatic dehumidification and intelligent drying of 3 IN 1 material, 3 IN 1 material mixture, 3 IN 1 polymer and several material mixtures;
3 IN 1 material is a plastic (resin) material. Because most 3 IN 1 engineering plastics are hygroscopic, coupled with the influence of weather and regional climate, it is easy for the plastic particles to become too wet to achieve the molding effect. In addition, in the previous granulation process, the plastic raw materials are different, so the moisture content and hygroscopicity are also different. Therefore, during the molding process, bubbles, silver bars, poor transparency, cracks and poor stability may occur, which seriously affect the quality of the product. The air duct of the 3 IN 1 desiccant dryer adopts a closed circulation system, which is not affected by the external weather. It can dry materials well in dry weather or wet weather without reversing moisture, and has high product molding quality.
The 3 IN 1 dryer first inhales the air in the environment to remove the moisture in the low dew point air, and then heats the dry air into one or more standard drying hoppers, thereby improving the drying efficiency and shortening the drying time. If the traditional hot air blower uses the moisture in the outside air to dry the material, it is difficult to achieve the drying effect. In addition, after the plastic or polymer is taken out of the moisture-proof sealed packaging bag and exposed to the atmosphere, it will begin to absorb moisture from the atmosphere. The traditional hot air blower cannot prevent the plastic from continuing to absorb moisture, and the drying effect is poor.
The use of 3 IN 1 material dryer can be divided into independent type and centralized type.
An independent 3 IN 1 dryer usually includes a dryer host, a drying barrel and a suction machine. The stand-alone dehumidification dryer is suitable for a small amount of various drying, and its advantages are high drying efficiency and convenient and quick material change.
The centralized 3 IN 1 dryer includes a drying host and several drying barrels.
Each drying barrel has an independent heating controller, which can dry several different raw materials at the same time, and cooperates with the air volume control valve to control the air volume of each drying barrel, which is suitable for mass production of plastics.
The working principle of this basic solution is: pour the cleaned and crushed plastic into the feeding box, start the motor, and the motor drives the first fan to rotate. When the first fan rotates, a large amount of airflow is generated, and the airflow gradually removes all plastic Blow into the spiral tube. Open the valve, the dry powder falls into the spiral tube, the airflow will blow the dry powder and the plastic at the same time, when the absorbent powder comes in contact with the water on the plastic, it will absorb the moisture. The output end of the motor can also drive the first gear to rotate, the first gear drives the second gear to rotate, the second gear drives the gear shaft and the worm on the gear shaft to rotate, the worm drives the worm wheel to rotate, and the worm wheel drives the rotating ring to rotate. When the plastic passes through the rotating ring with elastic strips, the elastic strips in the rotating ring will brush to the plastic and make the plastic rotate to change the direction, so that every surface of the plastic can contact with the dry powder and get dried. When the plastic passes through the rotating ring with a brush, the brush can brush off the dry powder contaminated on the plastic, and separate the plastic from the dry powder.
Product alias:3 IN 1 Compact Dryers |
3 IN 1 pellet dryer application
3 IN 1 Compact Dryers In the plastics processing industry, products appear shrinkage, silver streaks, bubbles, cracks, flow marks, poor transparency, etc. The main reason for these poor quality is that the plastics are not fully dried before they are molded. Engineering plastics such as : PA, PET, PC, PBT, CA and other materials with strong hygroscopicity, due to the penetration of moisture into the plastic particles, traditional hot air dryers cannot completely dry them. Practice has proved that reducing the dew point of the drying wind to below -40°C and controlling the heat to blow it over the surface of the moisture-containing plastic particles can reduce its moisture content to below 0.02% before molding. The three-in-one dehumidification dryer is airtight. The air is fully dehumidified and heated in the circulating system, and the dry air quickly completely separates the moisture in the plastic particles to achieve the effect of dehumidification and drying. 1. It integrates three functions of dehumidification, drying and two-stage feeding;
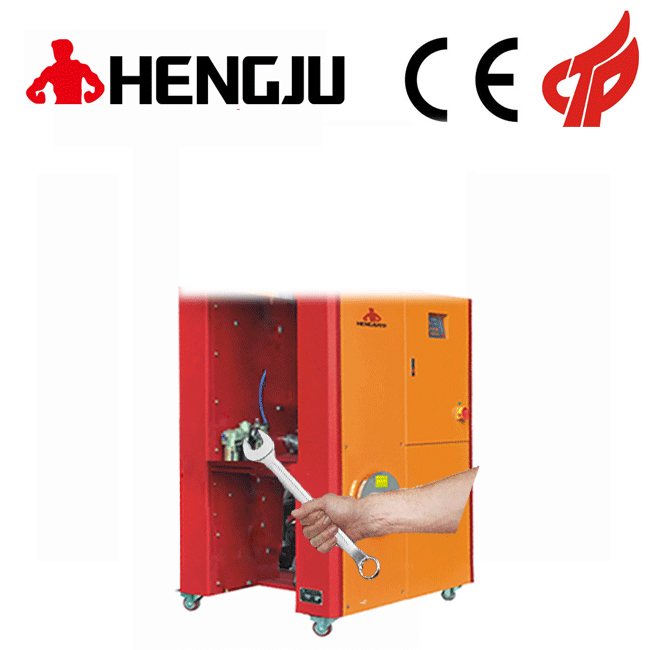 2. The dehumidification part is equipped with a wheel device, which can provide stable and low dew point air, and the dew point can reach below -40℃; 3. The stainless steel double-layer thermal insulation drying barrel adopts the design of lower blowing pipe to make the raw materials evenly dry and effectively prevent heat loss; 4. The feeding system is equipped with a shut-off valve to ensure that there is no residual raw material in the material pipe; 5. The closed loop feeding system can prevent the raw materials from being polluted or re-moisture; 6. The optical grade GCD-OP model is matched with a boiling electric eye hopper, which can remove the fine powder in the raw material, and can avoid pollution during the molding of optical grade products. Point generation; 7. The optical-grade GCD-OP model system is equipped with high-precision and high-efficiency filters, which can effectively filter dust ions up to 0.3μm, and the filtration rate is up to 99.9%; 8. PLC control with LCD touch man-machine interface can be purchased, the operation is centralized and convenient, and the whole machine can be controlled to run automatically; 9. Dew point detection device can be purchased; Relative humidity Relative humidity: The percentage of the actual water vapor density in the air and the saturated water vapor density at the same temperature is the relative humidity of the air. Dew point: Dew point: refers to the temperature of condensation of saturated water vapor in the air. At a relative temperature of 100%, the temperature of the surrounding environment is the dew point temperature. The dew point temperature is lower than the temperature of the surrounding environment, the less the possibility of condensation, which means that the drier the air, the dew point is not affected by temperature, but by pressure 3 IN 1 pellet dryer This is a device used to dehumidifying plastic resin to achieve drying. For example,
POM,ABS,TPE,PAL,ABS,CAB,EVA(2),EVOH,LM(4),LCP,PA11,PA6.46.6,PAI,PAR,PBT,
PC,PC/ABS,PC/PBT,PE.HDEPE,LDPE black3%,PE.HDEPE.LDPE black40%,PEEK,PE(1),
PEN,PES,PET,PETG,PI,PMMA,POM,PP,PPO,PPS,PS,[GPPS.EPS.HIPS],PSU,PIT,PUR,
PVC,SAN,SB,TPE,TPE,TPO,TPU,
3 IN 1 pellets dryer and other plastic resins must be dehumidified and dried during the production process to improve the quality of the finished product.
|
3 IN 1 pellet dryer Precautions
3 IN 1 pellets dryer 3 IN 1 Compact Dryers 1. Precautions for operation of desiccant dryer: 1.1. Make sure that the dehumidification dryer has been installed and adjusted; 1.2. Turn on the power switch on the control box power supply and the dehumidifier panel; 1.3. Check the temperature indicator of the material barrel frequently, and repair it in time if any fault is found; 1.4. When the temperature rises to the specified temperature, check whether it is consistent with the temperature of the lower part; 1.5. Keep 8 minutes full at any time during the production of the barrel; 1.6. The raw materials can be produced only after the specified drying time is fully reached; 1.7. When the drying is completed, when the machine is to be stopped, first close the feeding plate, and then close the feeding system after pumping the bottom raw materials. 2. Maintenance of dehumidification dryer: 2.1. Please confirm to provide cooling circulating water before machine operation; 2.2. Regularly clean the dehumidification return air aluminum mesh and the recycled motor aluminum mesh; 2.3. Regularly check whether the pipeline is damaged, loose, or dew; 2.4. Regularly check whether the floating belt is worn.Maintenance of 3 IN 1 desiccant dryer:
1. Record the daily operation and maintenance of 3 IN 1 desiccant dryer and establish files;
2. Regularly train operators, especially new employees;
3. Regularly maintain and maintain the single machine in the system;
4. Regularly check for leaks in conveying pipelines, especially vacuum pipelines and compressed air lines;
5. Clean the dust on the electrical parts of the equipment regularly.
Maintenance of 3 IN 1 granules dryer:
1. During the drying process of the material, all parts of the equipment in contact with the material need to be cleaned and sterilized;
2. The best operating temperature range of 3 IN 1 desiccant dryer is 15℃~40℃ to avoid excessively low or high temperature, which will affect the dehumidification efficiency or damage the equipment;
3. Regularly clean the central filter in the desiccant dryer, and replace it if it is damaged;
4. Clean the air filter regularly (about once every two weeks) to maintain the dehumidification and dust removal efficiency and life of the machine;
5. After cleaning the suction hopper and drying barrel, install them in place;
6. In order to improve the solubility, instant solubility, and dry products, they should be continuously discharged from the drying chamber quickly and packaged after cooling.
Doing the above maintenance work on the 3 IN 1 dehumidification dryer can reduce the probability of equipment failure, reduce maintenance costs, and effectively extend the service life of the 3 IN 1 pellet dryer.
Product alias:3 IN 1 dryer,3 IN 1 material mixture dryer,3 IN 1 polymer dryer |
|
|