plastic dryer,
Dehumidifying dryer,
Plastic pellet dryer,
plastic Dehumidifying dryer
Because some types of plastics need to be coaxed, the products that are printed will not have breaks, materials, and other reasons. With the widespread use of engineering plastics, dehumidification dryers are now gradually replacing traditional hot air blowers, and are increasingly used in the injection molding industry. They not only improve drying efficiency, but also ensure the final molding quality of products, which brings enterprises to production. Numerous benefits.
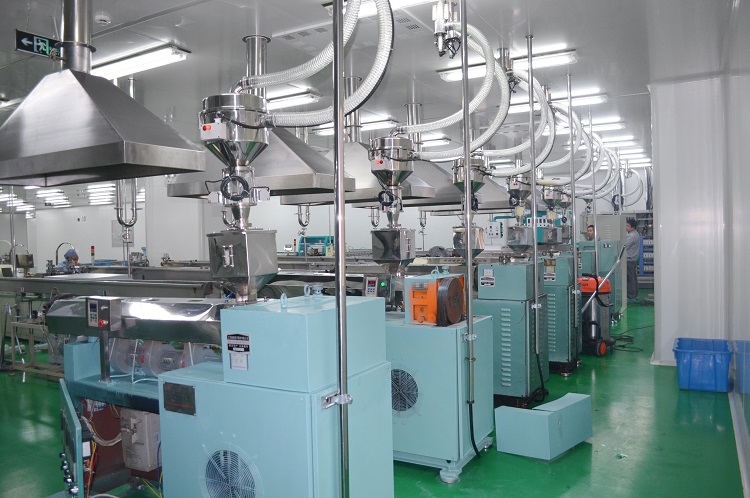
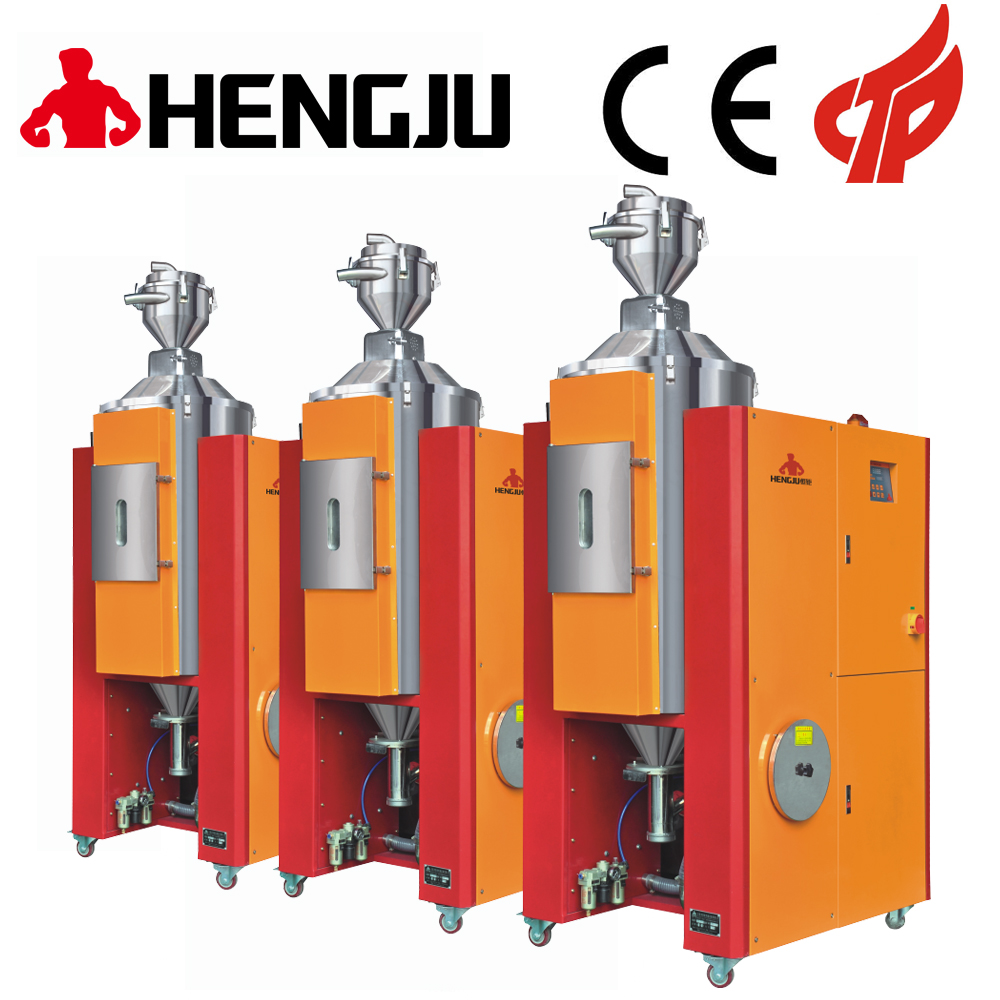 Why use dehumidification dryers in the extrusion industry and injection molding industry Plastics (engineering plastics) are different in the previous granulation process, so the moisture content and moisture absorption are also different. Therefore, when molding, it is easy to produce bubbles, silver bars, poor transparency, crack resistance, insufficient strength, and flow marks. Factors such as poor dimensional stability. Nowadays, most engineering plastics are hygroscopic. When the plastic is taken out from the moisture-proof sealed packaging bag and exposed to the atmosphere, it will begin to absorb moisture from the atmosphere. If it is a conventional hot-air barrel dryer, it is The external air with moisture is used to dry the plastic, so it cannot prevent the plastic from continuing to absorb moisture. In the process of dehumidifying the material, the movement of the material particles in the airflow is divided into an accelerated movement stage and a constant velocity movement stage. In the stage of acceleration, the sum of drag and buoyancy on the particles is greater than gravity, which has an upward acceleration. Therefore, the relative velocity of the particles and the airflow is a variable; as the velocity of the particles increases, the drag gradually decreases until 3 The vector sum of these forces is zero, and the particles enter the stage of constant velocity motion. At this time, the relative velocity between the airflow and the particles is a constant. The relative movement of the particles and the airflow has a great influence on the heat transfer rate between the particles and the airflow. In the initial drying stage, the ascent speed of the particles just enters the drying tube is zero, and meets the hot airflow with a higher speed to obtain upward At this time, the convective heat transfer coefficient between the two phases is very large, and the material particles continue to accelerate and enter the accelerated drying stage. The heat obtained by the solid particles in the accelerated stage accounts for more than half of the heat obtained in the entire drying stage. In the later stage of drying, when the rising speed of the solid material approaches or even reaches the airflow speed, the convective heat transfer coefficient is greatly reduced and the drying efficiency is reduced. In the drying process, changing the relative speed of the gas-solid phases, increasing the turbulence intensity at the boundary layer around the particles, expanding the contact area of the gas-solid phases as much as possible, and increasing the contact time of the two phases are effective measures to improve the drying efficiency.
plastic dryer,
Dehumidifying dryer,
Plastic pellet dryer,
plastic Dehumidifying dryer
|